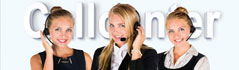
- 河南路港起重机有限公司
- 联系人:张总
- 17656156597
- 河南长垣起重工业园区
- www.lglmd.com
船用起重机在船舶事故中可能受到哪些影响?如何防范?
船用起重机作为船舶装卸作业的核心设备,其运行稳定性直接关系到船舶**与运营效率。在船舶碰撞、搁浅、火灾等事故中,船用起重机常面临结构损伤、功能失效等风险。本文结合典型案例与行业规范,系统分析事故影响机制,并提出针对性防范措施。
一、船舶事故对船用起重机的影响机制
碰撞事故中的结构损伤
船体剧烈震动导致起重机基座焊缝开裂,例如某货轮与码头碰撞后,起重机塔身出现3处贯穿性裂纹;
冲击波传递引发吊臂变形,某集装箱船碰撞后,吊臂弯曲角度达12°,超出设计容差;
电气系统短路,某油轮碰撞后,控制柜内40%的电子元件烧毁。
搁浅事故中的基础破坏
船体倾斜导致起重机重心偏移,某散货船搁浅后,起重机回转平台倾斜15°,引发液压系统泄漏;
泥沙侵蚀造成基座腐蚀,某拖轮搁浅后,起重机基座钢材厚度减少2mm,承载能力下降35%。
火灾事故中的热损伤
高温导致钢丝绳强度衰减,某滚装船火灾后,钢丝绳极限载荷下降*原值的60%;
液压油燃烧引发爆炸,某起重机液压系统油温超过200℃后发生爆燃,导致吊臂坠落;
电气元件失效,某起重机火灾后,PLC控制系统损坏率达85%。
恶劣海况下的运动耦合风险
纵摇、横摇导致负载摆动,某补给船在8级海况下,吊钩摆幅达5.2米,引发货物坠海;
升沉运动引发冲击载荷,某起重机在1.5米浪高下,钢丝绳动态载荷增加2.3倍。
二、典型事故案例分析
案例1:碰撞事故中的起重机损毁
2024年某货轮在进港时与拖轮碰撞,起重机基座焊缝撕裂,导致塔身倾斜18°。事故调查显示:
起重机未设置碰撞缓冲装置;
基座焊接质量未达ISO 5817标准;
船员未执行碰撞预警程序。
*终,起重机维修费用达1200万元,维修周期持续45天。
案例2:火灾事故中的液压系统失效
某起重机在装卸过程中因电气短路引发火灾,液压油泄漏后形成火势蔓延。事故分析显示:
液压系统未配备防火阀;
油管未采用阻燃材料;
消防系统未覆盖起重机作业区域。
导致起重机完全报废,直接经济损失超800万元。
三、防范措施与技术路径
结构强化设计
采用高强度钢材料,基座焊缝进行超声波探伤检测,确保焊缝等级不低于ISO 5817的B级;
安装减震装置,例如在基座与船体间设置橡胶隔振器,降低碰撞冲击力传递。
电气系统防护
关键电气元件采用防爆设计,例如使用Exd II CT4等级的防爆控制柜;
配备双回路供电系统,确保主电源故障时备用电源30秒内自动切换。
液压系统**
油管采用耐高温复合材料,爆破压力不低于20MPa;
安装油温传感器与自动灭火装置,当油温超过150℃时触发灭火系统。
运动耦合控制
采用主动防摆技术,通过加速度传感器实时监测船舶运动,调整吊臂姿态使负载摆幅<1米;
开发垂向补偿系统,使吊绳长度变化与接收船升沉运动同步,降低冲击载荷。
维护保养体系
实施“一机一档”管理,记录每次作业参数与维护记录;
每月进行液压系统压力测试,确保系统压力波动<±5%;
每季度开展电气绝缘检测,绝缘电阻值不低于0.5MΩ。
四、管理措施与应急预案
操作人员资质管理
要求操作员持有**海事组织(IMO)认证的起重机操作证书;
每年进行实操考核,考核项目包括负载定位精度、紧急制动响应等。
**检查制度
每日作业前检查钢丝绳磨损量,当直径减少量>7%时立即更换;
每月检测制动器摩擦片厚度,低于3mm时强制更换。
应急响应机制
制定起重机坠落应急预案,明确人员疏散路线与救援设备配置;
定期演练负载坠落事故,模拟钢丝绳断裂后吊臂坠落场景,训练人员应急处置能力。
技术改造升级
安装状态监测系统,实时采集振动、温度、载荷等数据,预警潜在故障;
采用数字孪生技术,构建起重机虚拟模型,预测运动耦合风险。
随着船舶自动化与智能化技术的进步,通过传感器融合与AI算法优化,可进一步降低船用起重机的事故风险,保障海上作业**。